Quality & Trace
Our Commitment to Quality Management and Pesticide Safety Standards
Sonoriku's agricultural products are grown by about 1,000 contract farms in and around the Nakhon Pathom province of Thailand.
All the farms observe strict standards and are obligated to obtain a certification known as the Thai GAP. It certifies that the farm is in good standing and practices sustainable production activities that ensure food safety, provide safe labor environments and take environmental conservation into consideration. Some farms have even obtained the GLOBALG.A.P. certification, which is an international standard. Furthermore, we have also obtained the HACCP and GMP certifications, which are international standards regarding food safety and quality management in factories.
In addition to the above, Sonoriku has its own management structure in place to monitor the use of pesticides. We conduct strict residue inspections so that we can deliver products with confidence to our customers.
Using Safe Pesticides
Japan's use of pesticides in agriculture is one of the highest in the world. When you hear the word "pesticide," you may automatically think how bad it is for our health, but sometimes we need them to grow high-quality crops.
The important thing is to inspect pesticide residue on products and to promote their safe and appropriate use.
At Sonoriku, we carefully select safe pesticides and train our farmers on how to use them appropriately. In this way, we are committed to delivering safe produce to our customers.
To Reduce Pesticide Residue
For the past 15 years, Sonoriku has been inspecting pesticide residue on products grown by our contract farms using our company-owned gas chromatography-mass spectrometer (GC-MS). In total, we have conducted 458 types of pesticide residue inspections at over 200,000 farms.
Residue inspections are meaningless if they are all done within a short, concentrated timeframe, or if they are only done every once in a while.
We conduct thorough inspections in accordance with a standard over an extended timeframe to ensure that the products we deliver are completely safe.
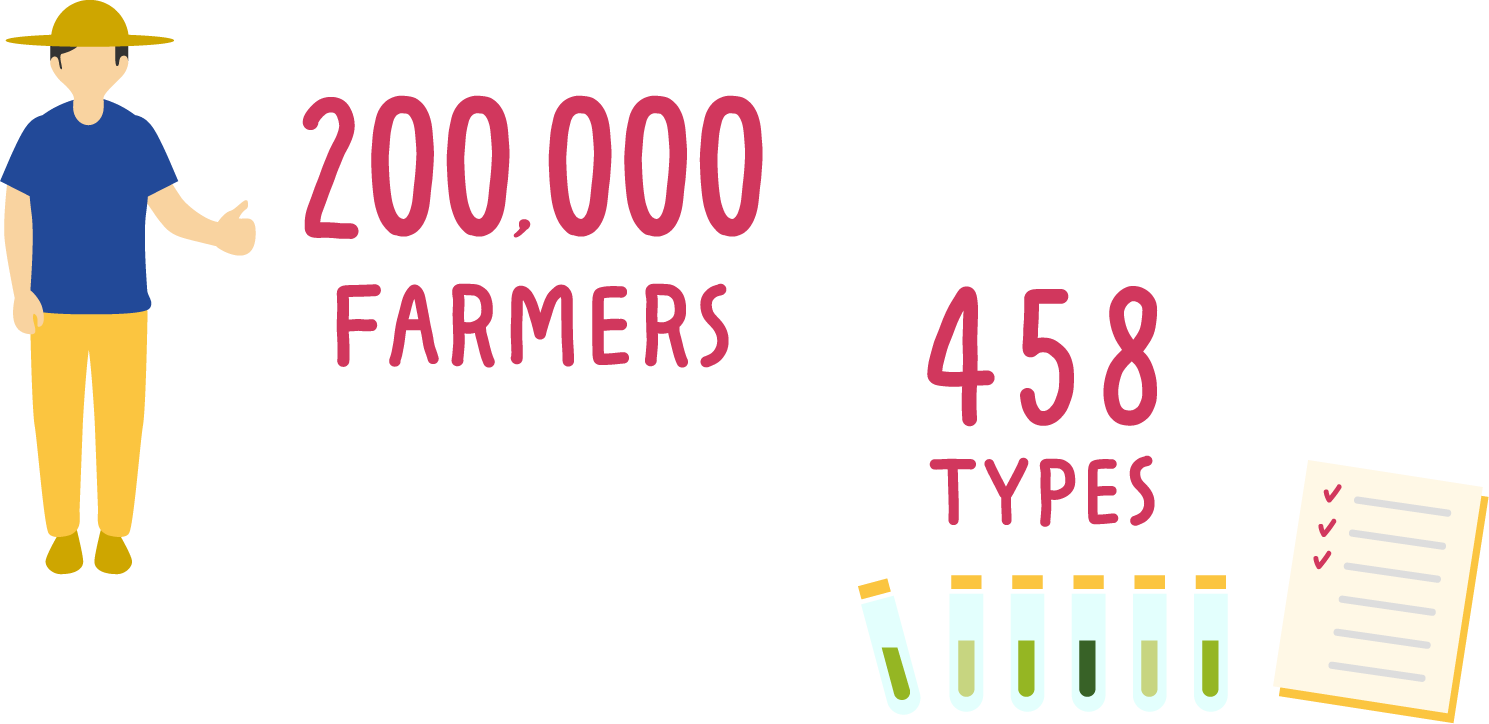
Analyzing the Causes of Excess Residue Levels and Undertaking Countermeasures
It is not enough to just check pesticide residue levels. When they exceed our standards, we must analyze the cause and resolve the issue.
For example, the most common cause is pesticide drift (unintentional diffusion of pesticide from a neighboring field). To counter this issue, we set up shielding nets between different crops that are planted within 5 m of each other. We also encourage farmers to always check on the status of their neighboring farmer's pesticide application.
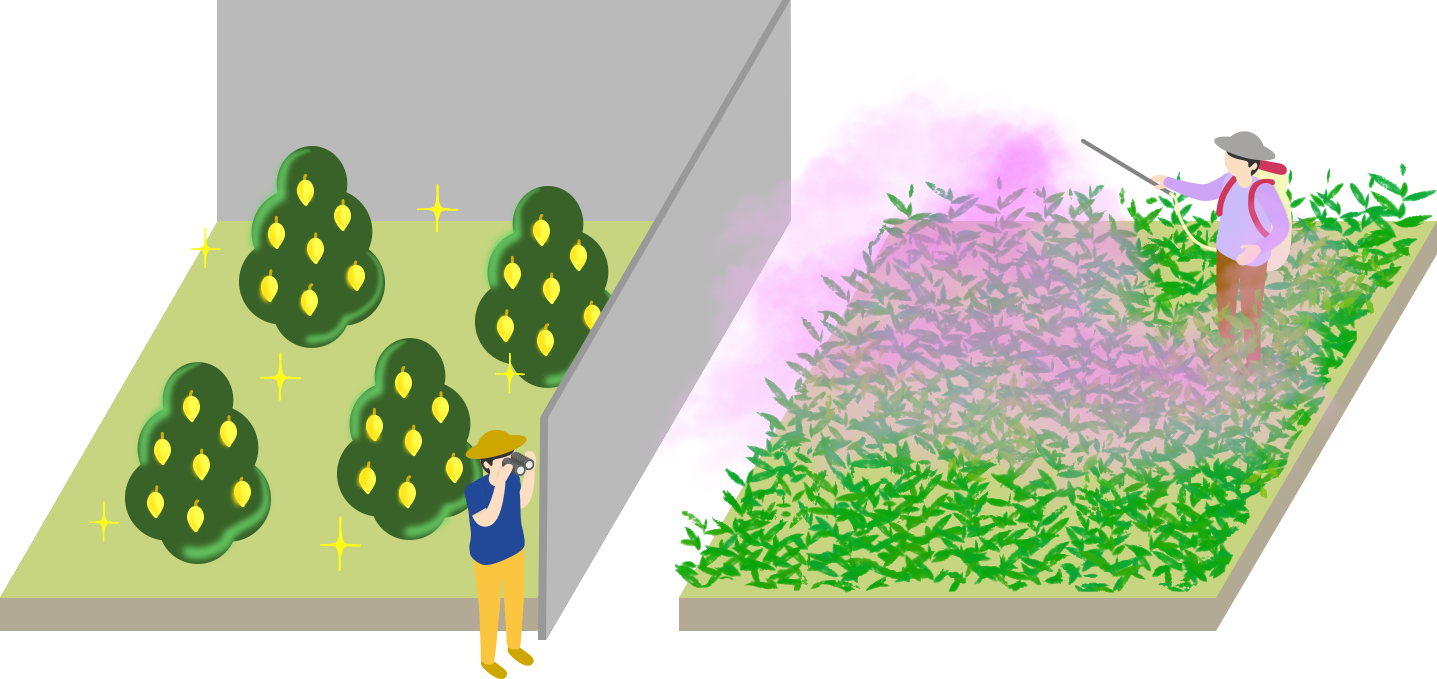
If we discover that a product we procured exceeds the pesticide residue standard, we immediately contact all the parties concerned. Within 30 minutes, all produce in the refrigerators that was bought from the farm in question is removed from the export line.
Furthermore, the field supervisor visits the farm within the same day to investigate the cause. Procurement from the farm is suspended from the following day and the farm is given a penalty. In this way, we are thorough in our strict management of quality.
This system ensures that only those products that the Sonoriku brand determines to be safe are delivered to our customers.
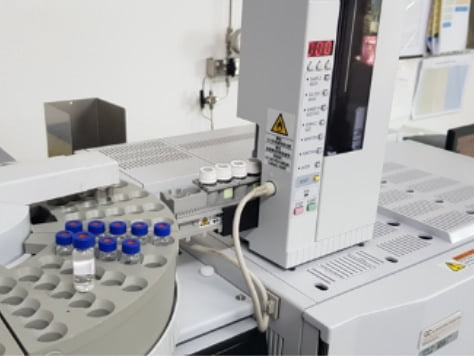
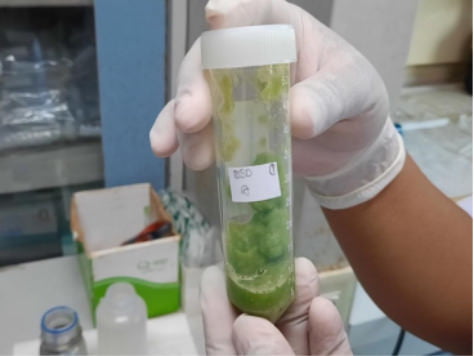
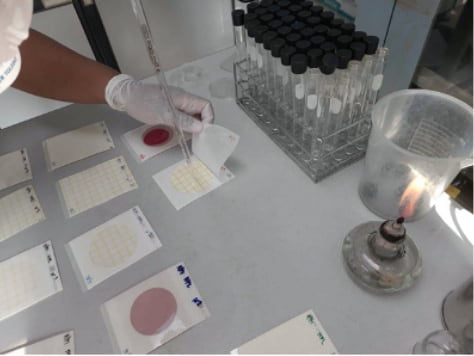
Training for Contract Farms
The detection of unauthorized pesticide residue can be caused not only by drift but also how pesticide sprayers are used and cleaned.
To prevent unintentional residue of such unauthorized pesticides, we hold our own training sessions for the farmers. Held jointly with universities and Thailand's Department of Agriculture, these large-scale training sessions are crucial to reforming the contract farmers' awareness and improving the quality of their crops.
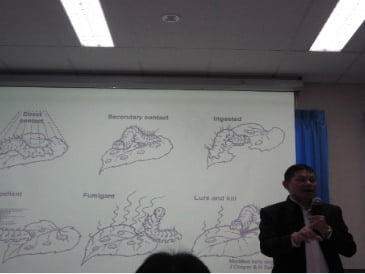
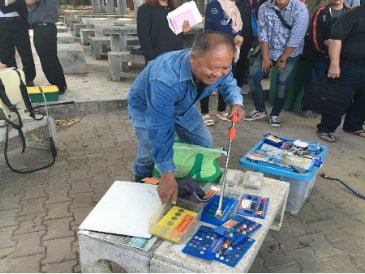
Our Strength Is Being Directly Connected to 1,000 Farms
Sonoriku has direct contracts with 1,000 farms, which amounts to 500 ha of agricultural land. This allows us to procure 3,000 t of crops a year to provide a steady delivery of high-quality products.
This solid network of connected farms is our strength. To maintain this strength, it is important that we put ourselves in the positions of each and every farm and be aware that we are growing the products together.

Quality Made Possible by Human Hands and Advanced Technologies
Highly experienced workers conduct manual inspections not only for insects and damage but also to sort and pack products according to size. This ensures more than just quality. It allows us to be an exporter of fresh produce that passes the plant quarantine inspections in Japan* with outstanding results. We have also been certified as an exporter that is exempt from inspections for okra, asparagus and mango. *Inspection to prevent pests from entering Japan
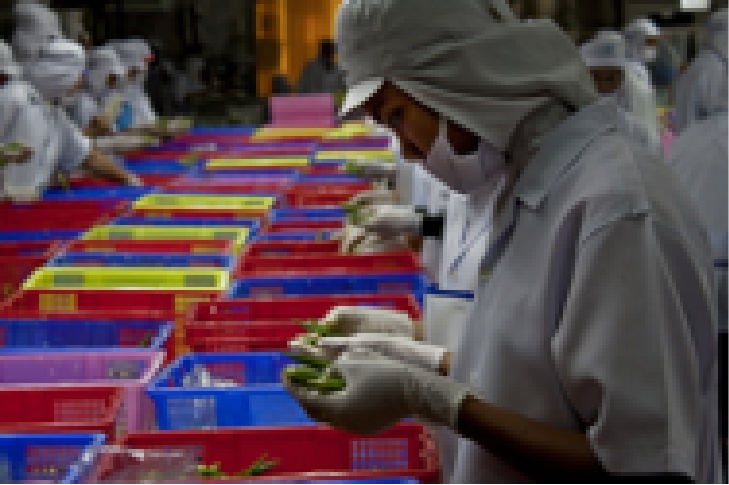
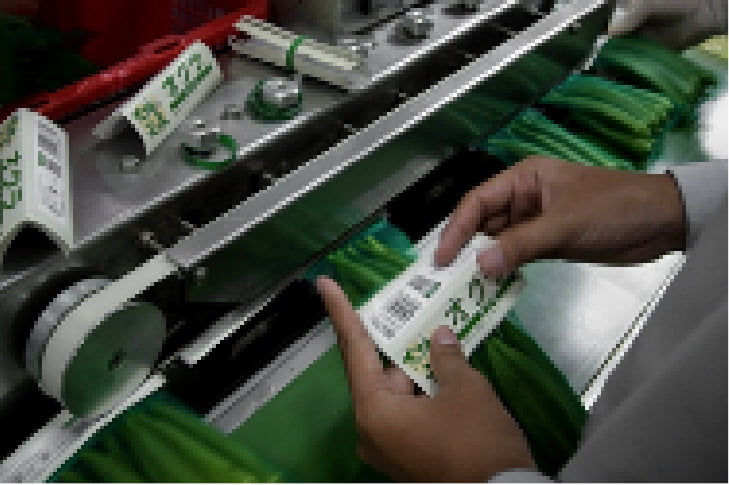
Strict Standards Observed by All Contract Farms
To deliver high-quality agricultural products as the Sonoriku brand, our contract farms, factory and logistics network are all required to clear strict standards and obtain licenses.
Obtaining a license issued by the Thai government not only improves quality but also motivates the farmers to take pride in their work.
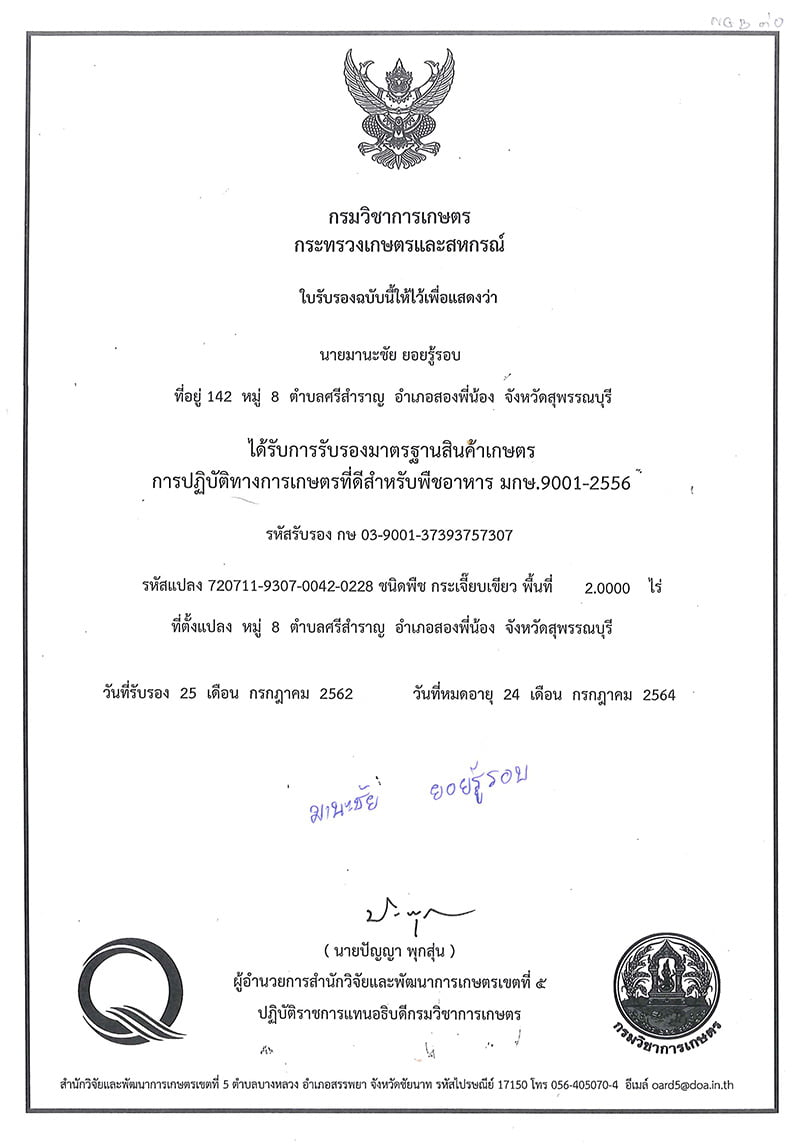
The Thai Good Agricultural Practice (GAP) was established as the equivalent of the GLOBALG.A.P. to certify farmers and promote agricultural exports. The certification provides management guidance and technical support to train Thai GAP instructors, contributing to the improvement of local product quality.
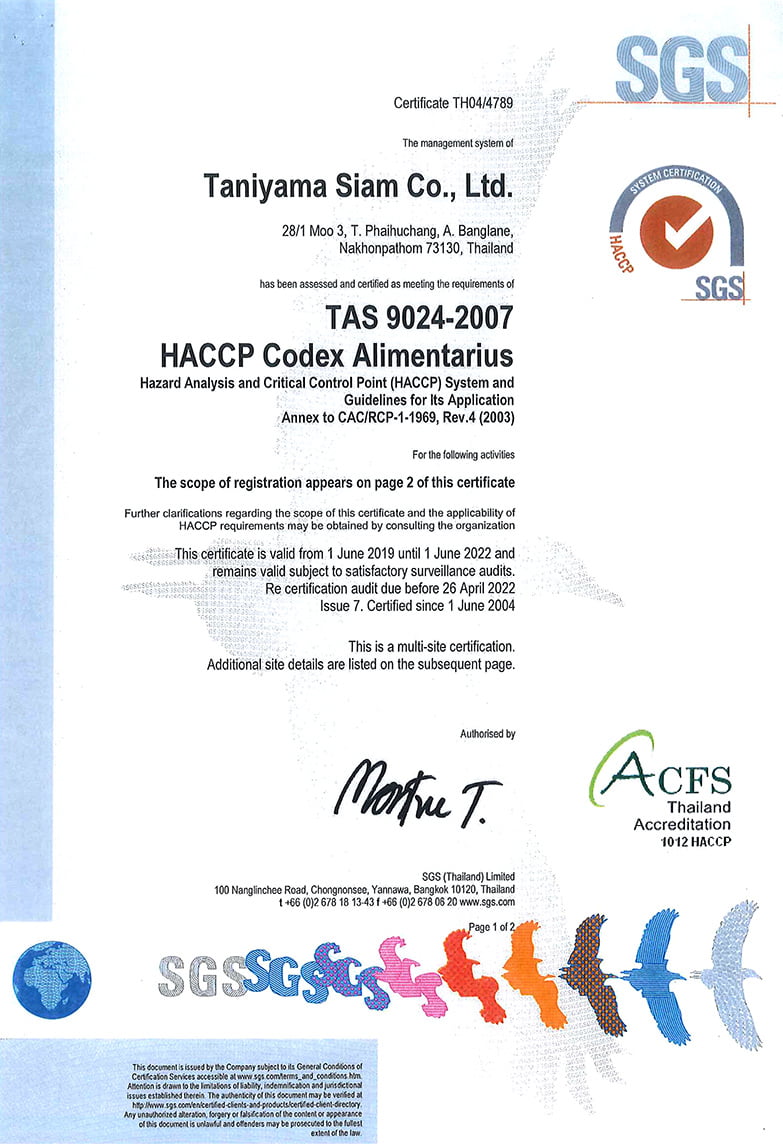
Hazard Analysis and Critical Control Point (HACCP) is a food safety management method that companies use to identify hazards such as food poisoning bacteria and foreign substance contamination in their products. Companies use the HACCP approach in all stages of the food chain, from procurement of raw materials to distribution of products, to manage the processes most crucial to eliminating or reducing such hazards. Compared to other food safety management systems that rely on sample inspections, the HACCP approach is more effective in preventing the distribution of products that contain issues.
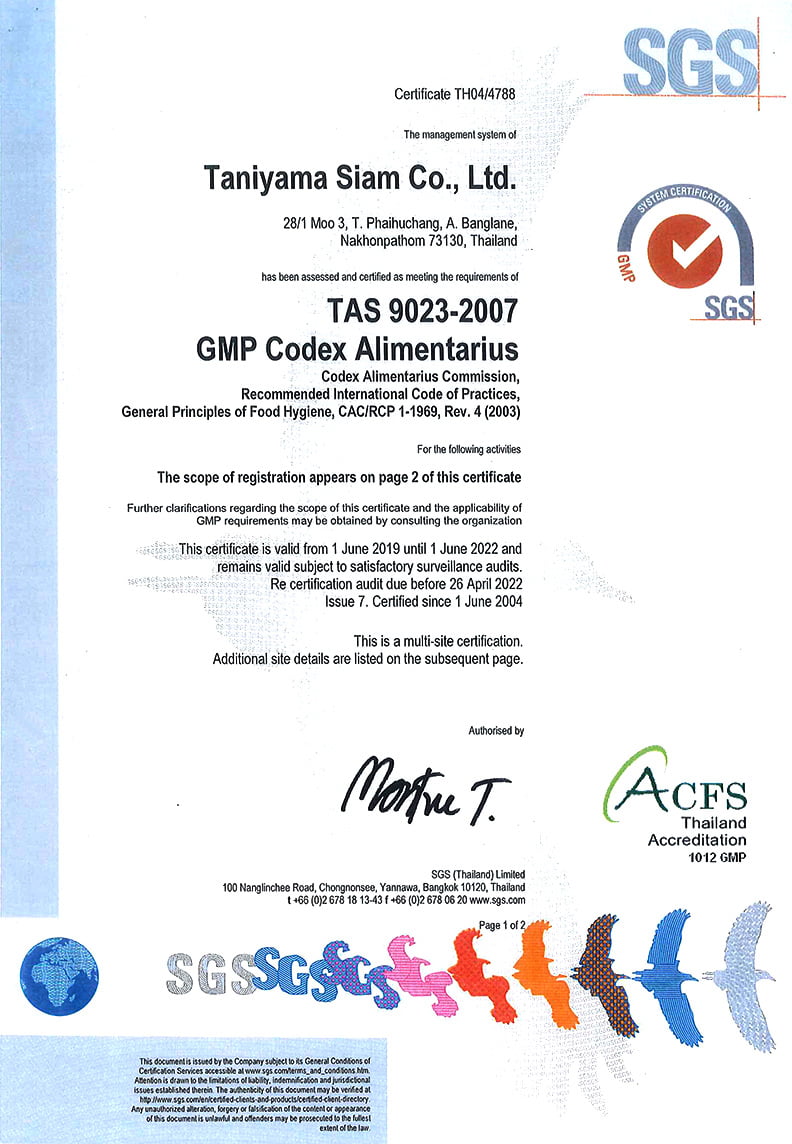
Good Manufacturing Practice (GMP) is a standard for food manufacturing management and quality management. It consists of criteria for appropriate management practices (manufacturing management and quality management standards) by manufacturers (including foreign manufacturers) and distributors. It involves the entire manufacturing process, from the procurement of raw materials to the shipment of finished products, in areas such as the factory's manufacturing facility, storage of raw materials, manufacturing processes, quality inspections, and food safety management. GMP is formulated by international organizations, such as the WHO, or regulators in each country.
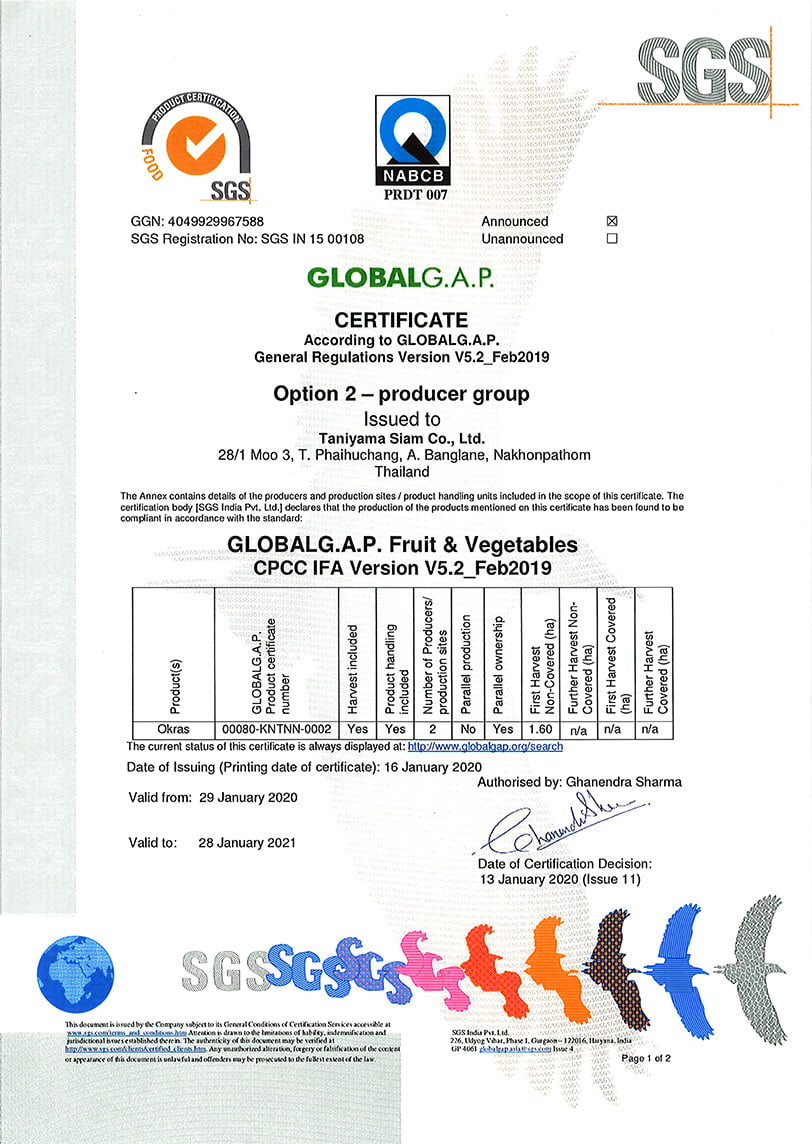
The GLOBALG.A.P. certifies that a farm is in good standing and practices sustainable production activities that ensure food safety, provide safe labor environments and take environmental conservation into consideration. As a general principle, farms are required to obtain this certification to export certain agricultural products to Europe.
Traceability
Our products can be traced throughout the food chain, from the procurement of raw materials to production to distribution.
By being transparent about where, when and by whom our products were made, we deliver delicious produce that our customers can enjoy with ease of mind.
If, by any chance, an issue arises after the shipment of the product, our system allows us to trace the product back to its raw materials, investigate and identify the cause of the issue and prevent future reoccurrences.
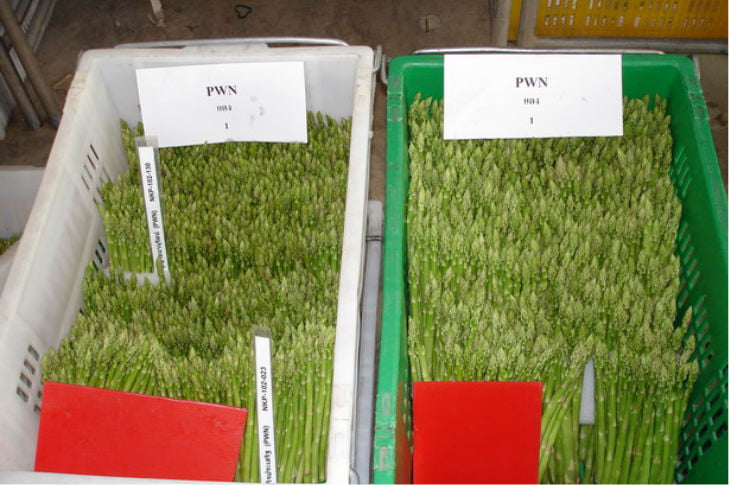
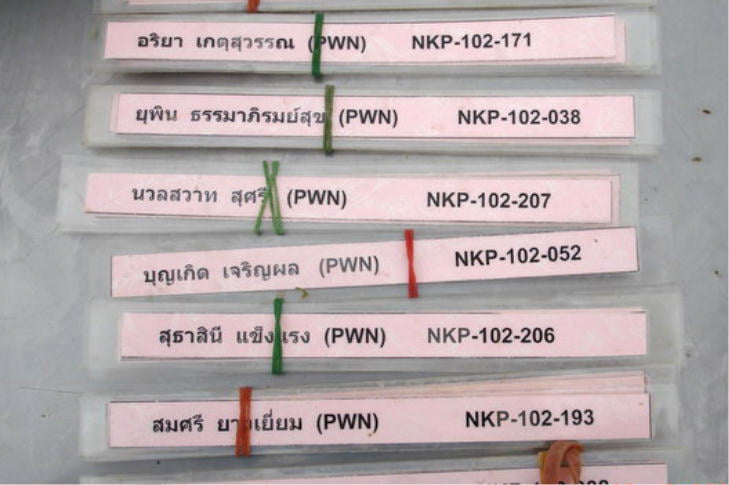
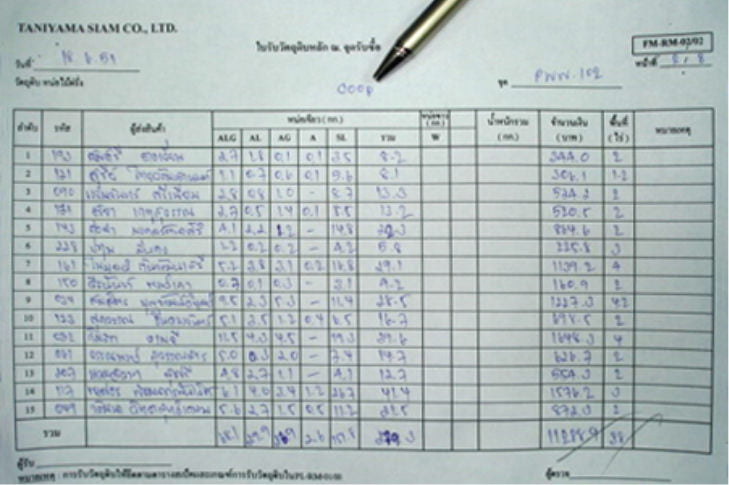
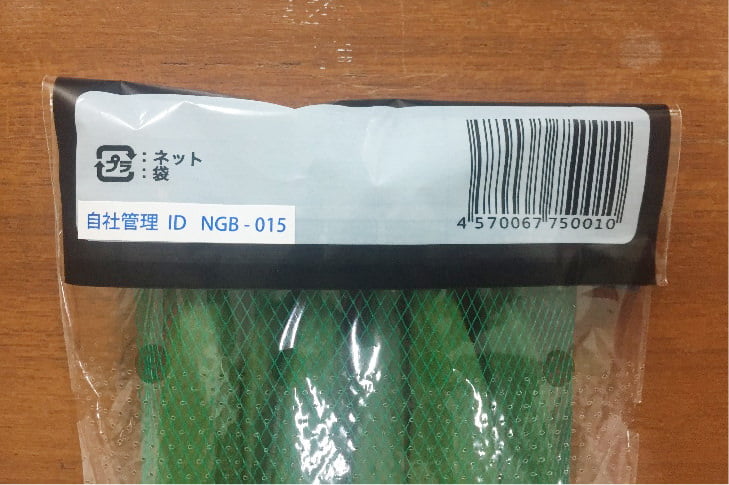